This article was originally written by Lauren Camilleri.
In the never-ending pursuit to boost bottom lines, businesses are more motivated than ever to find ways to reduce costs. When making equipment investments under constrained budgets, it is tempting to focus only on the short-term. However, the upfront price is only a small piece of the financial puzzle. Costs over an entire lifecycle can be significant when investing in large and technically advanced equipment like an off-highway engine. To understand the longterm value of an engine, it is imperative to evaluate not just the initial acquisition price but also maintenance, operating and disposal costs during ownership.
Doing so will reveal how investing in a superior engine design and comprehensive lifecycle support can take a meaningful bite out of total cost of ownership. Value is an often-discussed concept. Consider a midsize car. Sticker price is $20,000. Cost to own and operate it for five years? $43,500— more than double the purchase price. Smart new vehicle buyers consider fuel, insurance, maintenance and repair, as well as the length of time they plan to own the vehicle when making such a significant purchase.
Another way to look at value is examining longterm savings. The upfront price of installing triple pane windows is twice the amount of double pane windows. Factor in the increased efficiency and decades-long savings in energy costs and the scales tip the other way. It makes good financial sense to spend more upfront for a superior product when it offers better long-term savings.
Considering lifetime value is a must when purchasing an off-highway engine. This technical article will help equipment purchasers, owners and operators, along with facility and maintenance managers, gain a deeper understanding of an engine’s true value by examining total costs, their impact on lifecycle costs and the opportunities wise investors can leverage to benefit the bottom line.
In addition to comparing engine options prior to purchase, lifecycle costs are also often used as a basis for writing long-term service agreements, non-binding spare parts budgets and for general profitability analysis and planning.
Breaking down lifecycle costs
For an off-highway engine, lifecycle costs are comprised of four distinct cost categories: acquisition, operation, maintenance and disposal.
Acquisition
This non-recurring upfront cost is the initial engine or system purchase price, and typically includes installation and administrative costs including necessary facilities and training. The cost of an engine overhaul also falls into this category.
Operation
Fuel, lube oil and urea consumption are the primary contributors to operating costs, accounting for up to 90 percent of total lifecycle costs. This is especially true in mining or rail applications where the equipment endures high run hours.
Maintenance (preventive and corrective)
Savvy operators understand that planned maintenance and equipment availability go hand-in-hand. Preventive maintenance helps ensure peak performance, extend equipment life, and can even improve profitability.
Disposal
Costs also occur at the end of equipment life. Decommissioned engines must be removed and disposed of properly, in accordance with local regulations.
Acquisition
Upfront costs are easy for most people to grasp, which is exactly why their assumed contribution to total lifecycle costs is often overestimated. In terms of potential financial gains, or losses, the implications of an inaccurate lifecycle cost calculation can be quite significant—especially when considering equipment with a long life expectancy and high utilization rates. In these circumstances, often an upfront investment in higher equipment quality pays dividends over the life of that equipment in terms of lower operating costs.
Time Between Overhaul
Another important lifecycle factor to consider is time between overhaul (TBO), which refers to the overall life expectancy of an engine. TBO can be a difficult concept to grasp because some systems, such as MTU engines, are built to be overhauled as many as four times—giving operators four lives from a single engine. The important thing to keep in mind is that an engine has a life expectancy, and at the end of that expected life an operation can exercise one of three options: 1) scrap the engine and purchase a new one, 2) overhaul the existing engine and begin its “second life,” or 3) purchase a remanufactured engine from the factory and return the existing engine for a “core credit.” Each of these scenarios warrants a fresh look at LCC because it represents the start of a new engine life. New acquisition costs must be considered whether for a new engine, an overhaul or the expense of a remanufactured replacement engine.
Because MTU engines are built to be overhauled up to four times, MTU considers TBO as it would any other preventive maintenance activity. The end of the TBO refers to the point in time when an engine’s availability and reliability rates begin to decline due to wear. Overhauling at this point helps the owner/operator avoid the increased risk of potential failures, and restore their engine to like-new condition. MTU TBOs are estimated based on decades worth of field data and analysis based on engines with comparable load profiles and other life limiting factors.
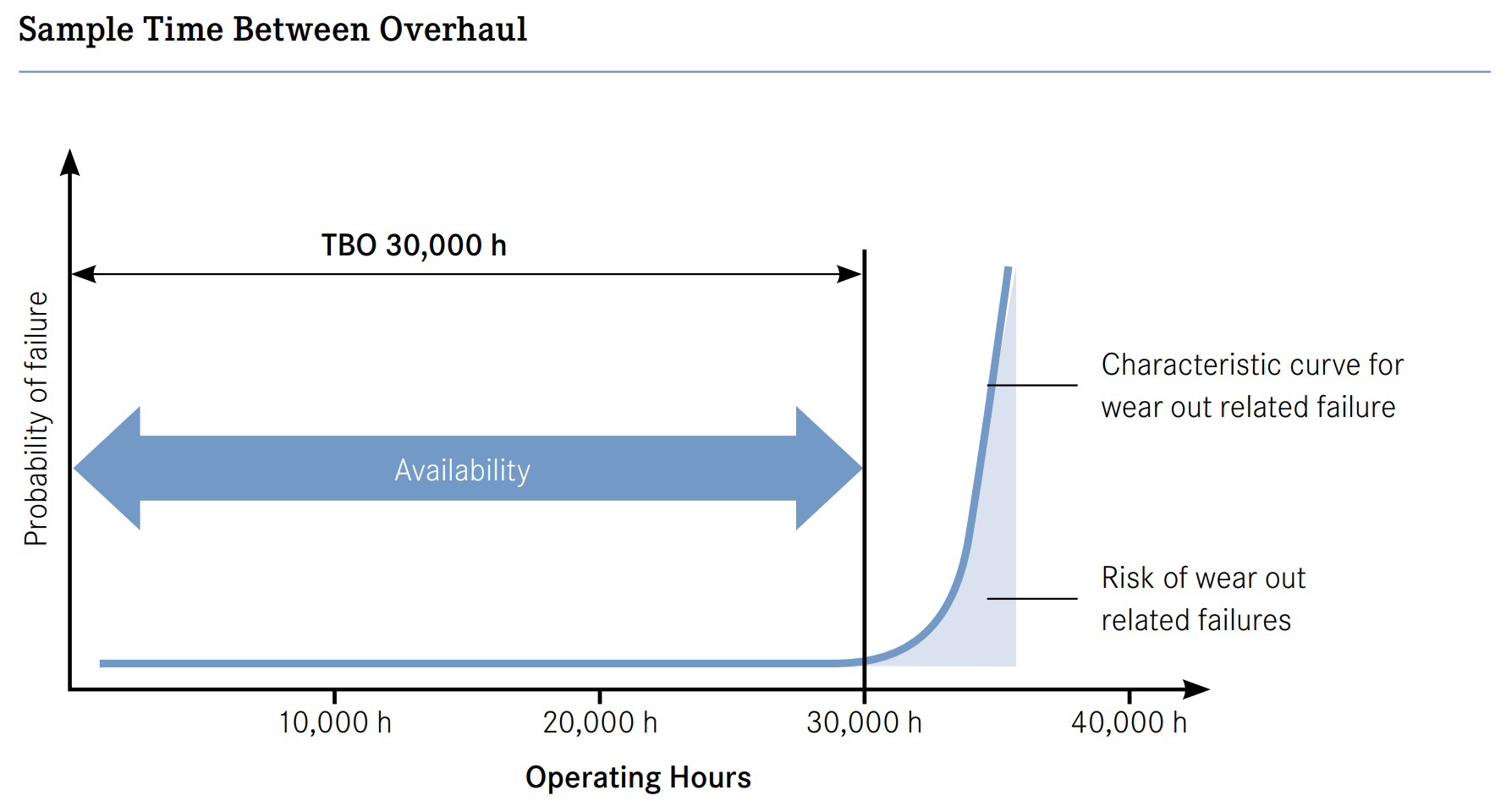
Operation
For off-highway engines, especially those operating in high run hour applications, the most significant contributor to lifecycle costs is operating expenses—primarily because of fuel. With the potential to account for as much as 90 percent of total lifecycle costs, it’s not hard to see why. Unfortunately, fuel is often one of the most neglected categories when evaluating overall value. Organizational silos can prevent purchasing analysts and decision-makers from understanding the critical role fuel plays in operating costs. When evaluating lifecycle costs and the potential purchase of an engine, it is critical to consider fuel—even a fraction of a percentage gain in fuel economy can yield tremendous savings throughout the life of an engine.
Maintenance
Maintenance and its related costs are also extremely important to consider when evaluating lifecycle costs, primarily because of the direct influence maintenance has over long-term operating costs and equipment life. Savvy operators recognize that proper maintenance throughout an engine’s life pays for itself and then some by extending equipment life and preventing declines in fuel economy and performance due to equipment wear. Unfortunately, a love-hate relationship often plays out between those who acquire operational assets and those who operate and maintain them. These often-siloed roles represent competing interests; one focused on maximizing profitability to meet short-term targets, which could mean deferring maintenance for short-lived savings. The other advocates for the continued investment in caring for valuable equipment—care that typically increases availability, improves equipment performance and extends equipment life. Given the fundamental role that equipment life and fuel economy both play in determining lifecycle costs, the gains achieved from a recurring investment in preventive maintenance must be considered alongside the costs of maintenance itself within any meaningful lifecycle cost calculation.
Disposal
Finally, it is important to factor in costs that occur at the end of equipment life. Decommissioned engines must be removed and disposed of properly, in accordance with local regulations. Repowered engine cores must either be destroyed or sent back to the manufacturer to be remanufactured and stamped with a new serial number. This critical step cannot be overlooked, as some operations in certain applications and geographies can face hefty fines that accumulate on a per-day, per-engine basis. With potentially high financial implications, mishandling a repowered engine core simply isn’t worth the risk.